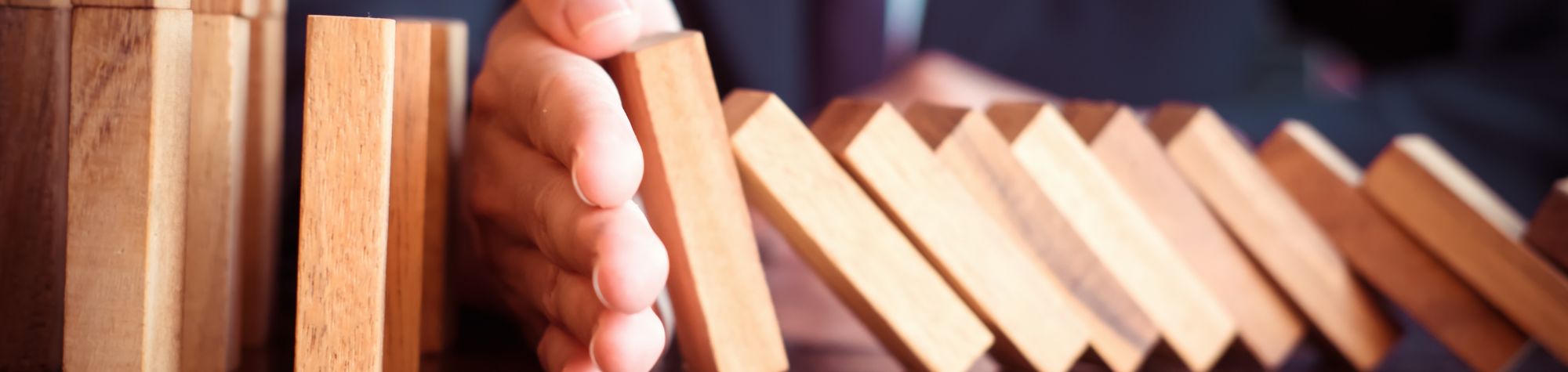
Construction projects are full of moving parts. How teams respond to issues can make or break timelines, budgets, and relationships. While some wait until problems happen before taking action, others plan ahead to avoid disruptions. These two approaches—reactive and proactive—are central to how construction projects are managed. With tools like Building Radar providing early insights into thousands of projects, making proactive decisions has never been more accessible.
Moving from a reactive mindset to a proactive strategy significantly improves efficiency and reduces costly errors. By combining predictive data, clear communication, and early warnings, proactive construction helps minimize rework, delays, and disputes. Building Radar’s global market intelligence empowers teams to spot risks earlier and create contingency plans with confidence.
Understanding Reactive construction
Reactive construction management responds to problems after they arise. It focuses on quick fixes and short-term solutions rather than planning ahead. While reactive actions are sometimes necessary—especially during unforeseen events—they often lead to increased costs and stress.
Typical reactive scenarios include:
- Addressing a safety incident after it happens
- Rerouting deliveries when materials are late
- Fixing design errors after construction begins
- Hiring emergency subcontractors to cover delays
Addressing risks only after they happen typically results in higher costs to fix issues and increased project delays. Rushed responses may also compromise the quality of work and materials used. Additionally, delayed actions can reduce stakeholder confidence in the project’s success. These inefficiencies affect scheduling, budgeting, and communication across the board.
The Proactive construction approach
Proactive construction aims to prevent problems before they occur. It involves early planning, forecasting, monitoring, and communication to keep the project on track.
Key proactive practices include:
- Performing risk assessments before work begins
- Using AI tools to forecast potential delays or weather impacts
- Holding pre-construction coordination meetings
- Implementing checklists for quality and safety
MASTT highlights that proactive teams achieve better cost control and fewer incidents. Proactive methods also improve team accountability and help align project outcomes with stakeholder expectations.
Comparing Proactive vs. Reactive in construction
Understanding the pros and cons of both approaches helps project managers choose the right strategies at different stages.
1. Project risk
Reactive construction often increases project risk due to unpredictable responses. Proactive planning reduces uncertainty and allows for faster, controlled decision-making.
2. Cost Impact
Delays, rework, and emergency responses drive up costs in reactive projects. Proactive planning, by contrast, identifies cost-saving opportunities and reduces waste.
3. Communication
Reactive teams tend to communicate in crisis mode. Proactive teams create a communication plan early and use centralized tools to keep everyone aligned.
4. Time Efficiency
Proactive methods support smoother workflows and early task execution. Reactive methods often cause stop-and-go progress and extended timelines.
5. Quality Control
Proactive planning ensures quality inspections are scheduled and followed. Reactive projects may overlook quality issues until it’s too late to fix them affordably.
Real-world example: Delays from material shortages
A reactive team might only notice a missing shipment after the site halts. A proactive team using Building Radar’s supply insights could forecast delays in advance, contact alternative suppliers, and keep work moving. With access to tenders from 400+ platforms and real-time data, proactive teams stay informed and agile.
How Proactive practices reduce costs
Delays, safety issues, and design errors are expensive. Proactive management helps detect problems during planning stages, when solutions are cheaper and simpler to implement. Integrating Building Radar with planning tools enhances this by allowing teams to spot trends and risks based on 45+ customizable filters.
Building Radar: Empowering Proactive construction
Building Radar helps teams take control of their pipeline by enabling early identification of relevant projects. With access to +1000 new tenders daily across 100+ countries, construction professionals can spot opportunities and risks before competitors do. Teams using the platform have reported a +310% increase in win rate from early engagement to order—proving the power of proactive planning.
Used by over 150 companies worldwide, Building Radar provides the insights needed for smarter outreach and forecasting. Its AI-powered features help contractors qualify leads faster, identify key decision-makers, and uncover high-value projects. Clients have already gained $2.3B+ in order volume and +20% profitability by shifting toward proactive construction strategies.
Proactive means Prepared
Whether managing a small build or a multinational project, choosing a proactive construction approach leads to better outcomes. From reduced risk to greater efficiency, the benefits are clear. Tools like Building Radar give teams the confidence to act early, plan smarter, and deliver stronger results.
Relevant Links
- From Reactive to Proactive: Shifting Gears in Construction Project Management
- Early Warnings: From Reactive to Proactive in Construction
- Proactive vs Reactive Risk Management: Which is Better for Construction?
- Construction Market: UK
- Construction Market: Brazil
- Construction Market: China
- Building Strong Contractor Relationships
- Sales Enablement Skills
- Top Material Producers
- Construction Material Insights